Company: TechNH, Inc.
Industry: Custom Injection Molding
Employees: 55
Shifts: 3 (Sunday 11 PM – Friday 11 PM)
Setting the Mold
TechNH, a New Hampshire-based custom injection molding manufacturer, produces precision-molded parts for the medical, industrial, and consumer markets. The company made a significant operational leap by implementing DELMIAWorks Manufacturing ERP software. This change represented a notable upgrade for TechNH, moving them from a static database to a fully integrated, real-time operational system.
In combination with their internal resources, the company needed a dependable, knowledgeable partner they could trust to guide hardware selection, configure devices, and support ongoing system integrations and upgrades. Enter, IMS.
Hot Spots & Pressure Points
Prior to migrating to DELMIAWorks, TechNH operated with limited automation — relying heavily on manual inventory tracking and management. The move to an ERP system required a complete infrastructure upgrade, including rugged mobile computers, barcode scanners, industrial label printers, and enterprise-grade wireless networking to capture and communicate data reliably across two buildings, three shifts, and a variety of production and warehouse activities.
In addition, TechNH serves as a parts supplier for both government and medical molding customers. This role demands strict traceability and process control. To meet these requirements, the company needed a solution capable of:
- Tracking lot codes of raw materials; including resins
- Monitoring production and inventory movements in real time
- Capturing data at every stage — from receipt of materials through finished goods shipments
- Ensuring full visibility of materials for traceability and compliance reporting
The combined implementation of DELMIAWorks ERP, modern data capture devices, and a robust wireless infrastructure enabled TechNH to meet these demands while streamlining operations and improving overall process control.
shaping operations
IMS stepped in as a strategic advisor, providing:
- Expert hardware recommendations: IMS guided the team in selecting Honeywell CK Series rugged mobile computers, which impressed not only TechNH but also their ERP implementation specialist, who began recommending the devices to other clients.
- Seamless configuration and integration: From initial setup to ongoing support, IMS ensured that mobile computers and barcode scanners were properly configured to support real-time data capture in DELMIAWorks.
- Upgrade and lifecycle management: When TechNH upgraded their ERP version, IMS proactively reconfigured devices, ensuring zero downtime for their third-shift team and providing on-site support during the go-live weekend.
- Consultative best practices: IMS continues to advise TechNH on expanding data collection processes to the shop floor, enabling operators to enter production data directly and improving accountability and traceability.
Tooling Up for Success
The partnership between TechNH and IMS has delivered tangible, lasting improvements across TechNH’s manufacturing operations. By integrating real-time data capture with reliable mobile technology, the company has gained greater visibility, control, and agility on the shop floor and in the warehouse. These enhancements have not only optimized day-to-day processes but also positioned TechNH for future growth and scalability — ensuring their operational infrastructure is as precise and dependable as the products they manufacture.
TechNH has realized a number of benefits from this transition overall, but some of the highlights that keep operations moving along steadily, include:
Real-Time Inventory Management: All inventory movements, from production to shipping, are now tracked via Honeywell CK Series mobile computers, offering complete visibility and traceability — particularly vital in maintaining their medical manufacturing standards.
Improved Accountability: Operators are now responsible for scanning and recording their own transactions, reducing bottlenecks and human error. With every product tailored to a customer’s unique specifications, accurate inventory management is vital to their operation.
Operational Continuity: IMS’s rapid, reliable service ensures that when issues arise, they’re resolved without disrupting production or shipping schedules.
System Scalability: When TechNH is ready to upgrade to next-generation Honeywell devices, they can leverage compatible tools and accessories along with IMS’s expertise to ensure a smooth transition.
Enhanced Efficiency for Management: With DELMIAWorks and IMS’s hardware integration, TechNH’s management team benefits from real-time reporting, streamlined data collection, and reliable device performance — reducing administrative burden and allowing leadership to focus on strategic growth initiatives.
Customer Stamp of Approval
“IMS has been an incredibly knowledgeable and competent resource for us. It’s a huge relief knowing that if there’s a problem, we don’t have to stress about troubleshooting — we know it’s handled. Their recommendations have been spot-on, and they make sure our systems are ready when we need them,” said Anna Sullivan, Director of Finance, TechNH
READY TO CALL IN REINFORCEMENTS FOR YOUR OPERATIONS?
Our team is here to help. Contact us today to schedule a no-obligation consultation.
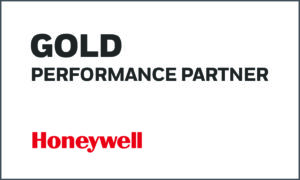